Sumitomo Rubber to Begin Proof of Concept Toward Harnessing Hydrogen Energy at Shirakawa Factory in Fukushima Prefecture ~Part of Our Ongoing Efforts to Achieve Carbon Neutral Tire Manufacturing~
Jul. 28. 2021
Sumitomo Rubber Industries, Ltd. is pleased to announce that, with the backing and support of the New Energy and Industrial Technology Development Organization (NEDO, a national research and development agency), our major tire factory in the City of Shirakawa (Fukushima Prefecture) will begin a proof of concept from August with the ultimate aim of harnessing hydrogen energy, which is widely hailed as a safe and clean next-generation energy source of the future, in tire manufacturing.
1. Objectives
・To establish techniques for harnessing hydrogen as a new source of energy with the ultimate aim of achieving carbon neutral tire manufacturing.
・To establish a model for local production for local consumption by utilizing hydrogen produced within Fukushima Prefecture.
・To develop tires that emit zero*1 CO2 during production processes.
2. Background
Tire manufacturing requires the application of high-temperature, high-pressure heat energy in the form of steam, which is difficult to produce using only electric power due to various technical limitations. Thus, the Sumitomo Rubber Group has turned our attention to hydrogen as a promising new energy source for our ongoing efforts to achieve carbon neutrality. And so, we selected Shirakawa Factory as a pilot factory to demonstrate hydrogen’s potential while taking advantage of existing programs to harness hydrogen energy that are already underway in Fukushima Prefecture. We then submitted this plan to NEDO, who selected it for backing and support.
3. Future Plans
With support from NEDO, Shirakawa Factory will conduct a proof of concept that involves harnessing hydrogen energy in certain tire production processes from August 2021 through February 2024. Thereafter, we plan to expand the use of hydrogen energy throughout Shirakawa Factory and, ultimately, to our group factories in Japan and overseas.
4. Proof of Concept Overview
This proof of concept will involve harnessing hydrogen energy for production processes involved in NEO-T01*2 (a proprietary tire manufacturing system that we first established in 2012) while studying the challenges involved in maintaining 24/7 continuous production using hydrogen energy. Through the process of identifying and enacting countermeasures to overcome various technical challenges, such as how to control nitrogen oxide emissions when using a hydrogen boiler, we hope to demonstrate the effectiveness of hydrogen as a safe and clean energy source to eventually replace the conventional energy sources currently used in tire manufacturing.
At the same time, with an eye toward our increased demand for hydrogen following the completion of this proof of concept, we will also be examining various possibilities for producing hydrogen using electric power generated from other renewable energy sources as well as for the procurement of carbon-free hydrogen as part of our efforts to minimize CO2 emissions throughout a tire’s lifecycle.
In December 2020, the Sumitomo Rubber Group established “Our Philosophy,” a new corporate philosophy framework that will serve as a major driving force to propel us forward with ever greater speed toward the accomplishment of our groupwide business strategy while placing particular emphasis on engaging in sustainable business activities that promote harmonious coexistence with society and with the natural environment. Our Philosophy defines our Purpose (i.e. the very reason for our existence) thusly: “Through innovation we will create a future of joy and well-being for all.” With this Purpose serving as the basis behind our every decision and as the impetus behind our every action, the Sumitomo Rubber Group will continue working to enhance not only our economic value, but also our value to society so that we may contribute to the development of a more sustainable society.
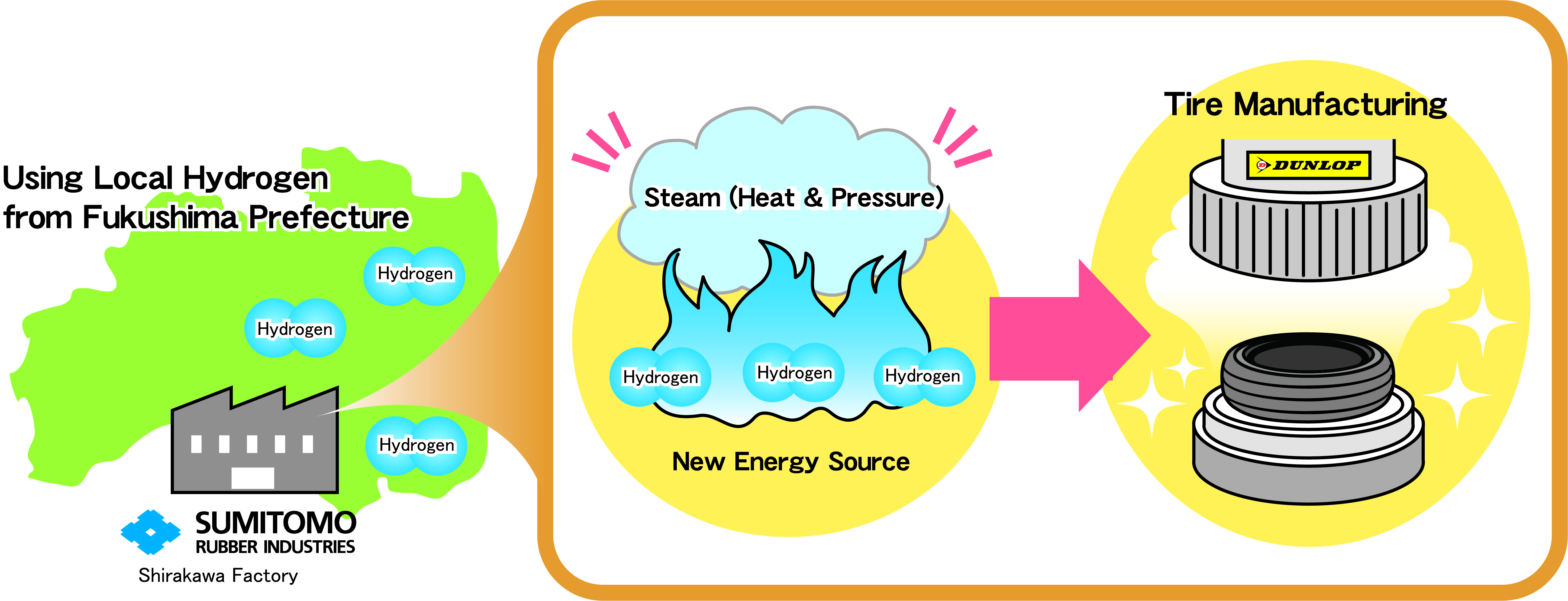
1. Objectives
・To establish techniques for harnessing hydrogen as a new source of energy with the ultimate aim of achieving carbon neutral tire manufacturing.
・To establish a model for local production for local consumption by utilizing hydrogen produced within Fukushima Prefecture.
・To develop tires that emit zero*1 CO2 during production processes.
2. Background
Tire manufacturing requires the application of high-temperature, high-pressure heat energy in the form of steam, which is difficult to produce using only electric power due to various technical limitations. Thus, the Sumitomo Rubber Group has turned our attention to hydrogen as a promising new energy source for our ongoing efforts to achieve carbon neutrality. And so, we selected Shirakawa Factory as a pilot factory to demonstrate hydrogen’s potential while taking advantage of existing programs to harness hydrogen energy that are already underway in Fukushima Prefecture. We then submitted this plan to NEDO, who selected it for backing and support.
3. Future Plans
With support from NEDO, Shirakawa Factory will conduct a proof of concept that involves harnessing hydrogen energy in certain tire production processes from August 2021 through February 2024. Thereafter, we plan to expand the use of hydrogen energy throughout Shirakawa Factory and, ultimately, to our group factories in Japan and overseas.
4. Proof of Concept Overview
This proof of concept will involve harnessing hydrogen energy for production processes involved in NEO-T01*2 (a proprietary tire manufacturing system that we first established in 2012) while studying the challenges involved in maintaining 24/7 continuous production using hydrogen energy. Through the process of identifying and enacting countermeasures to overcome various technical challenges, such as how to control nitrogen oxide emissions when using a hydrogen boiler, we hope to demonstrate the effectiveness of hydrogen as a safe and clean energy source to eventually replace the conventional energy sources currently used in tire manufacturing.
At the same time, with an eye toward our increased demand for hydrogen following the completion of this proof of concept, we will also be examining various possibilities for producing hydrogen using electric power generated from other renewable energy sources as well as for the procurement of carbon-free hydrogen as part of our efforts to minimize CO2 emissions throughout a tire’s lifecycle.
<Shirakawa Factory Profile>(Current as of December 31, 2020) | ![]() |
|
Location Start of Operations Scope of Operations Production Capacity (New Rubber Consumption) Employees |
: Shirakawa, Fukushima Prefecture : 1974 : Manufacture of Tires for Passenger Cars, Trucks & Buses : 10,350 Tons/Month : 1,595 |
|
Shirakawa Factory | ||
In December 2020, the Sumitomo Rubber Group established “Our Philosophy,” a new corporate philosophy framework that will serve as a major driving force to propel us forward with ever greater speed toward the accomplishment of our groupwide business strategy while placing particular emphasis on engaging in sustainable business activities that promote harmonious coexistence with society and with the natural environment. Our Philosophy defines our Purpose (i.e. the very reason for our existence) thusly: “Through innovation we will create a future of joy and well-being for all.” With this Purpose serving as the basis behind our every decision and as the impetus behind our every action, the Sumitomo Rubber Group will continue working to enhance not only our economic value, but also our value to society so that we may contribute to the development of a more sustainable society.
※1. | Achieving zero CO2 emissions in tire manufacturing will involve using solar power in combination with hydrogen energy. |
※2. | NEO-T01 is a high-precision “Metal Core” manufacturing system that achieves balanced high performance in terms of “Riding Comfort,” “Environmental Friendliness” and “Safety” by combining three key technologies: (1) The “Metal Core Process,” in which the various components of a tire are applied one by one to a metal former (core) that has been made in the exact shape and size of an actual finished tire’s inner liner; (2) “Fully Automatic Connected Control,” which utilizes a computer control system to control the application of each tire component to the Metal Core with ultra-high precision, accurate to 0.01mm; and (3) “High-Rigidity Structure,” which allows for the use of more rigid reinforcing materials than conventional tire manufacturing techniques. |