Chapter01水素エネルギーでタイヤを作る
タイヤの製造は、ゴムと薬品の「混合」、タイヤ部材の「製造」、部材の「組み立て」、加熱と加圧で化学反応を起こし数種類のゴムを一体化してタイヤにする「加硫」、さらに「検査」「出荷」の主に6つの工程を経るが、このうち熱源を欠かすことができないのが加硫工程だ。加硫には100℃を超える高温・高圧の蒸気が必要だが、蒸気を作り出すために化石燃料の天然ガスを用いるため、CO2の排出が避けられない現状がある。これが、タイヤ製造におけるカーボンニュートラルの最大のハードルとなっていた。
タイヤの製造工程
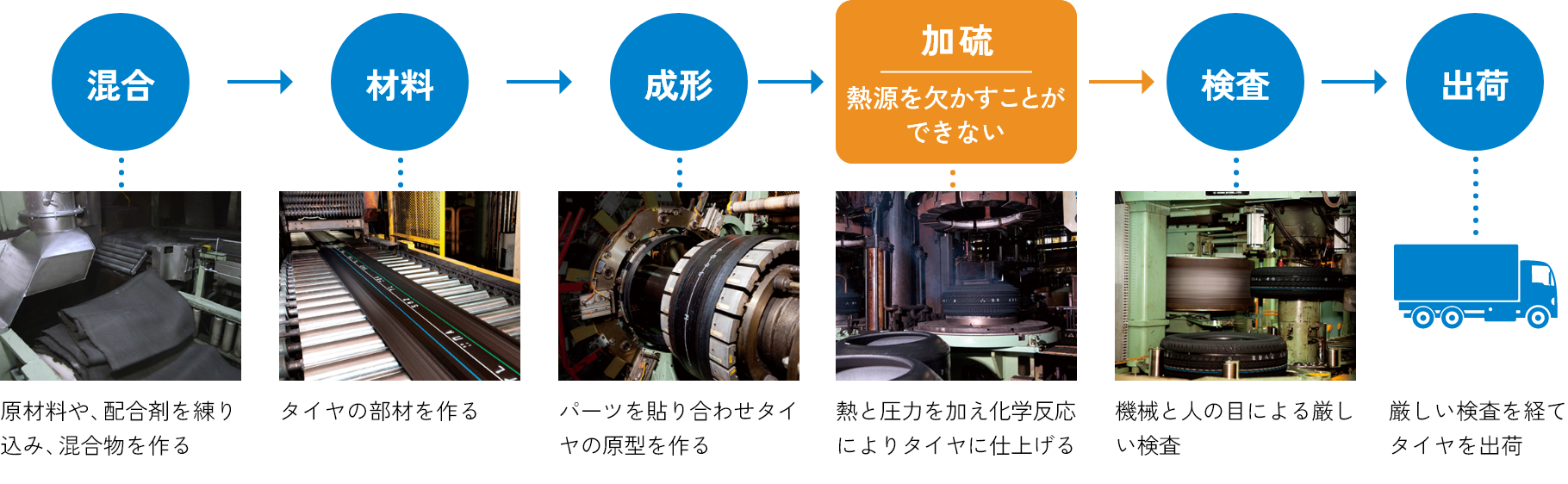
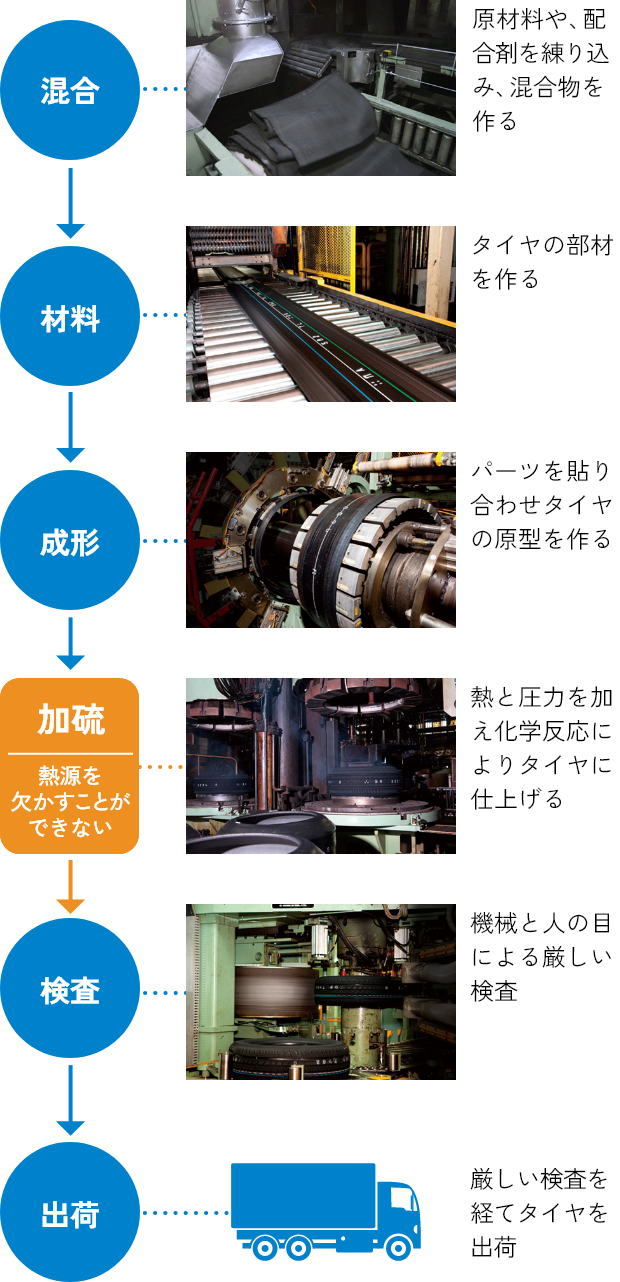
「温室効果ガスの排出を削減するため、白河工場では省エネルギーの取り組み、2つのエネルギーを同時に生産し供給するコージェネレーション(熱電併給)、太陽光発電などに取り組んできました。しかし、これらの取り組みだけでカーボンニュートラルは実現できません。特に加硫のための高温・高圧の蒸気を電力で発生させることが技術的に難しい中で、どのように加硫工程でCO2の排出を減らしていくのか、大きな課題となっていました」と話すのは、白河工場環境管理課課長で工務課の業務も兼任するK.T.。これまで白河工場や名古屋工場、さらに中国や南アフリカの工場でも設備導入に携わってきた大ベテランでさえ、当初は加硫工程のカーボンニュートラル化は想像が難しかったという。「部署内や本社の設備技術部とも意見を交わし、検討する中、クリーンエネルギーとして注目を集め始めていた水素がその候補に挙がりました。タイヤ製造の方法を大きく変更することなく、既存の設備を利用できるなど、蒸気発生の熱源として最も現実的かつ効果的だったのです」。
カーボンニュートラルへの取り組み
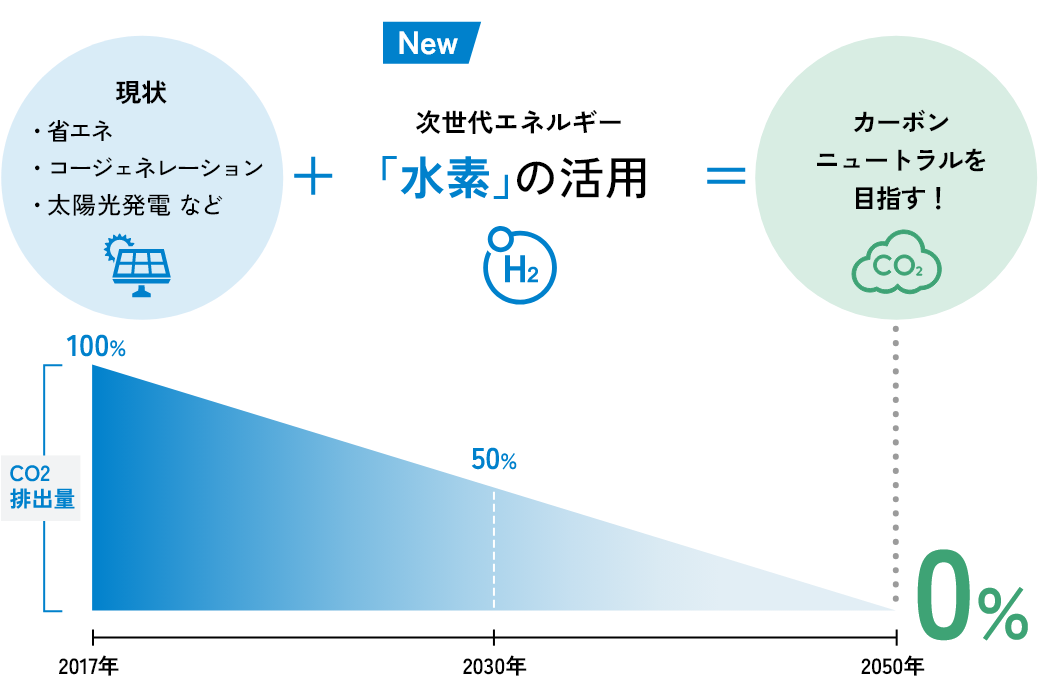
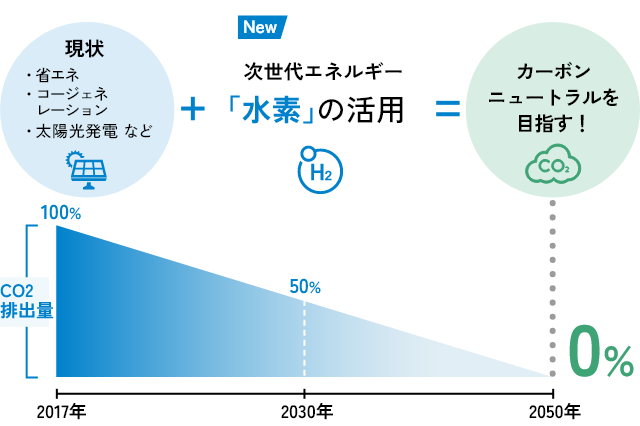
水素は電気を使って水から取り出せるほか、さまざまな資源から生成することができ、燃焼させて熱エネルギーとして利用してもCO2を排出しない。実際、製鉄所や化学工場などでは副次的に発生した水素の二次利用も行われている。その一方で、水素は熱量が小さいため、タイヤ製造に影響がないのか、必要な蒸気を発生させるだけの量の水素が確保できるのか、コストはどうかなど、実現に向けた検討項目は数多くあったとK.T.は話す。「部署のメンバーや本社の設備技術部等の関連部署と実現の可能性を一から探りながら、徐々に『水素ならできる』という手応えを得て、プロジェクトが形となっていきました。水素は供給側の研究が進む一方、実際に活用する需要家側の実証研究はほとんど例がなく、水素の利用が難しい中、地域の行政と水素供給会社の協力を得ることができたことからNEDO*1の助成事業に応募し、2021年8月から、白河工場でタイヤ製造における水素エネルギー活用の実証実験がスタートしました」。
K.T.は2022年7月に立ち上がった工場内の環境管理課でプロジェクトをリード。実証実験における主任研究員の立場でもあり、スケジュール管理や各部署からの意見の集約・調整といった実証実験全体を取りまとめる役割を担い、水素エネルギーの導入を推進している。「最初からすべての燃料を水素エネルギーに代替することはできません。今回の実証実験では、住友ゴムの最新タイヤ製造システム「NEO-T01*2」の加硫工程に水素エネルギーを活用しています。工場で使う燃料の数パーセントを水素エネルギーでカバーするものですが、未来につながる技術を得るための最初の一歩です。まだ誰も実現したことのない、最先端の技術を確立するためのチャレンジに、年甲斐もなく毎日ワクワクしています。これまでの経験を活かし、設備導入のアドバイスを行っていますが、若手社員から出てくる柔軟なアイデアから学ぶことも多く、いい刺激を受けています」。
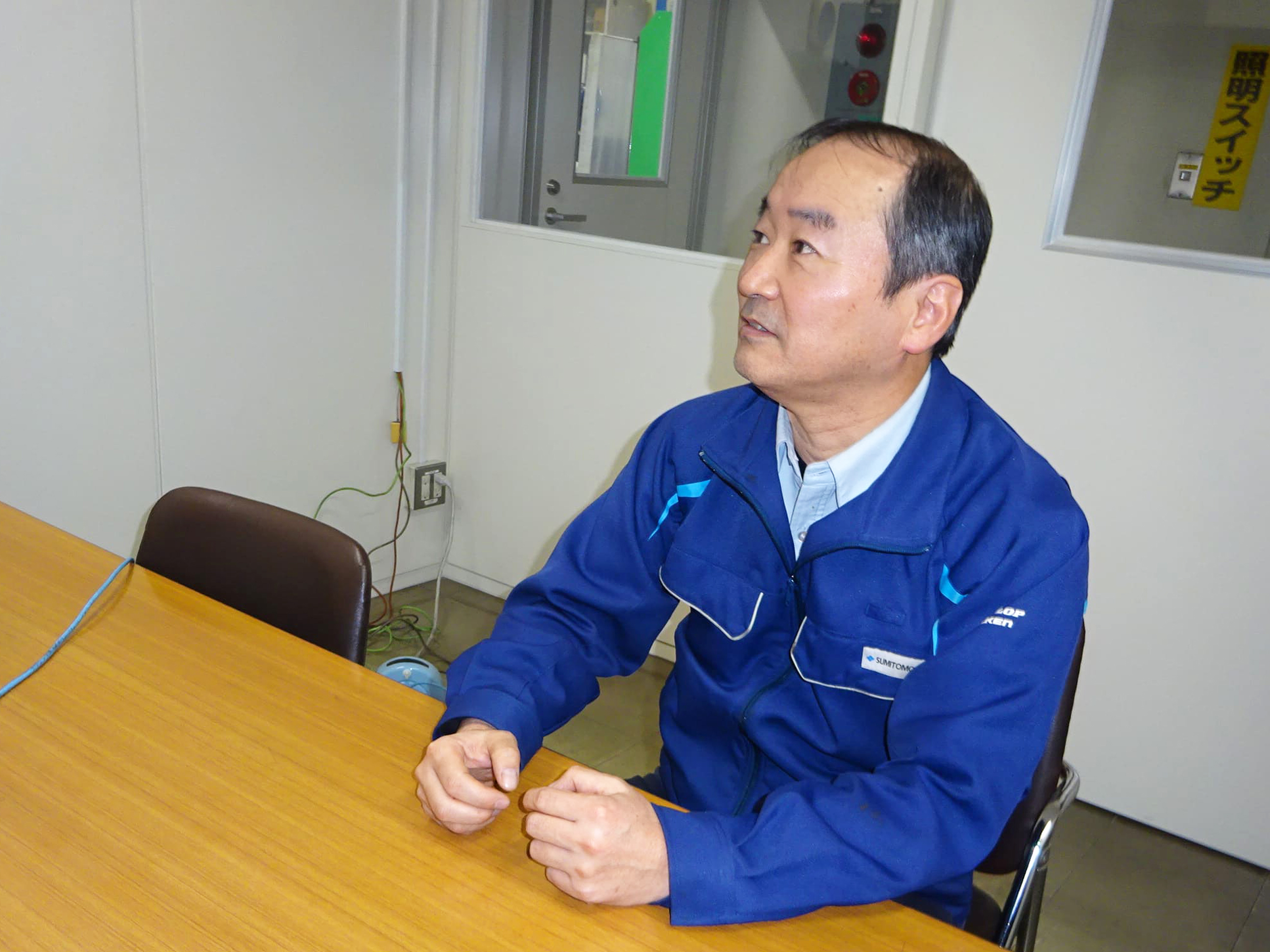
*1 NEDO:国立研究開発法人新エネルギー・産業技術総合開発機構
*2 NEO-T01:「快適性能」「環境性能」「安全性能」を高次元で実現する高精度メタルコア製造システム。(1)実際の仕上がりのタイヤサイズで作られているタイヤ内側の形状をした金属の成形フォーマーにタイヤの各種部材を貼り付けていく「メタルコア工法」、(2)メタルコアへの部材貼付けを100分の1ミリ単位のコンピュータ制御システムによってコントロールする「全自動連結コントロール」、(3)従来より強靭な素材を補強部材とする「高剛性構造」、という3つのキー技術を用いた工法。
Chapter02水素エネルギーの活用を具体化する
K.T.が属する工務課は各工場に配置され、工場内の設備導入やメンテナンス、改良などを行っている。K.T.と同じく、現在は白河工場環境管理課に所属するW.S.は、2015年の入社後から白河工場工務課の一員として加硫工程の設備管理、動力のエネルギー管理などを担い、工場のISO14001*1審査対応にも尽力。エネルギー管理士の資格を持つ、動力エネルギーマネジメントのエキスパートだ。水素エネルギーの導入にあたっては計画の初期段階から参画し、設備の導入などを牽引している。「最初は燃料に水素を使うと言っても、周りはネガティブな反応が多かったですね。二次利用はあっても、わざわざ水素を購入してエネルギーにするような需要家はほぼ皆無でしたし、水素は爆発する危険なものだというイメージを持っている人も多くて…。でも、経済産業省が水素社会の実現に向けたロードマップを策定する中、将来水素社会が現実になった時、住友ゴムにはこの技術は必要だと思いました。住友ゴムはもちろん、広く製造業を見渡しても初となるチャレンジでしたが、どんな時もK.T.さんが『それいいね、やってみようよ』と私のアイデアの実現を支え、アドバイスをしてくれたことは、とても心強かったです」。
蒸気を作り出す水素ボイラーをはじめとした設備の具体的な能力やサイズ、設備レイアウト、配管などを検討していくプロセス設計、国や県が指定する高い安全基準を満たすための法令管理、設備導入の際の工事管理など、W.S.の役割は多岐に渡る。「スケジュールがある中、社内はもちろん、ボイラー機械メーカーや設備工事業者など、多くの人を巻き込むプロジェクトでしたので、正直、プレッシャーはありました。でも、プロジェクトの目的や意義を話すと、多くの人がこの技術に興味を持ち、私たちと同じ想いを持って取り組んでくれたことはうれしかったです。ちょうど先日水素ボイラーが設置され、いよいよ火が入る段階にまでたどりつきましたが、技術的な手応えはかなり感じています。実証実験の結果次第で、社会的にも大きなインパクトを与えることになるはずです」。
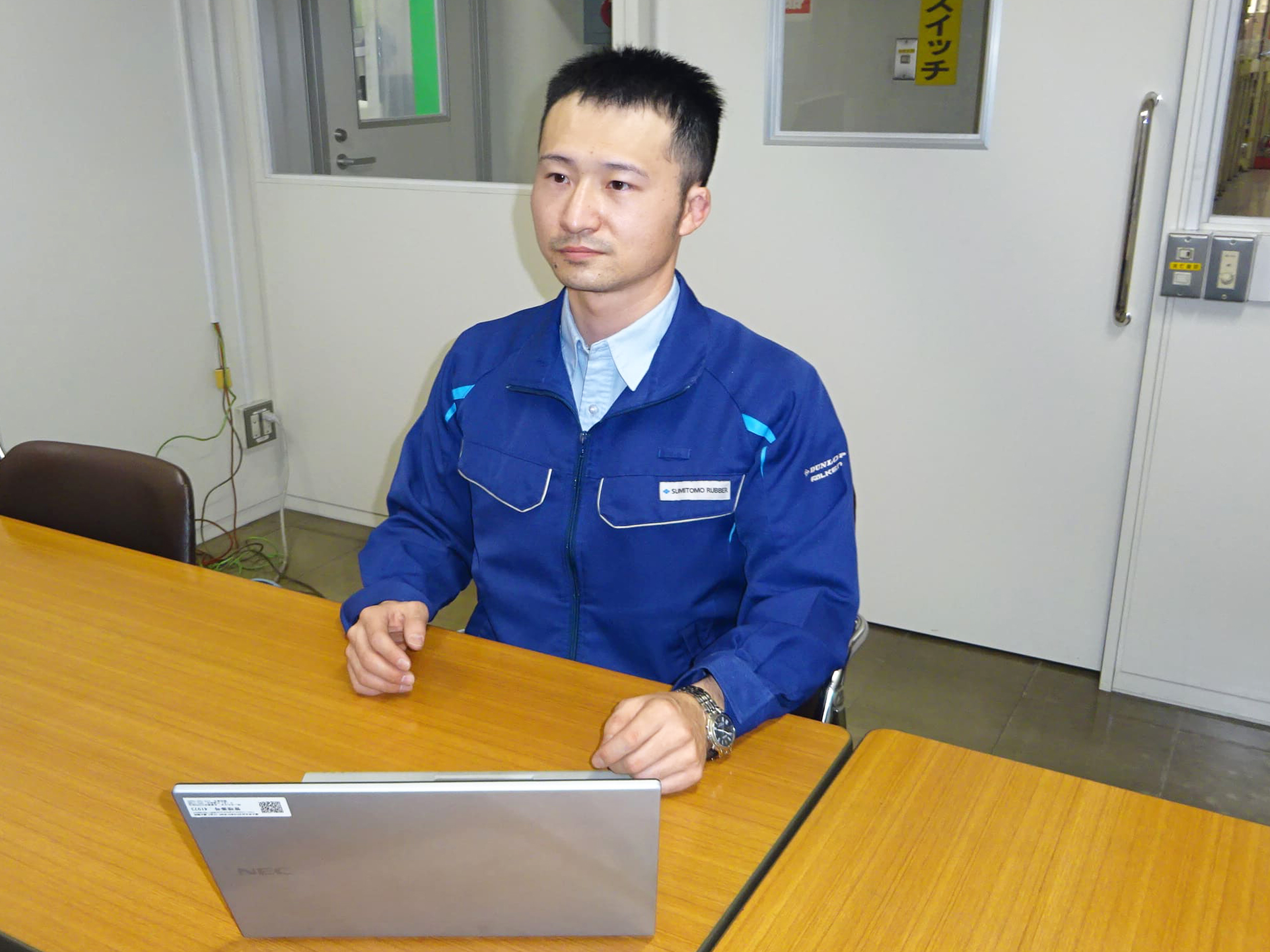
*1 ISO14001:環境を保護し、環境パフォーマンスを向上させるためのマネジメントシステム規格
Chapter03前例のないチャレンジを支える
水素エネルギーの導入には、白河工場環境管理課とともに本社の設備技術部も大きく関わった。設備技術部は製造の効率化や技術展開を行うために各工場を俯瞰的に管理し、設備導入のサポートや技術調査などを行っている。設備技術部で動力部門を担当するM.M.は、2016年の入社後に白河工場工務課に配属し、W.S.と一緒に動力設備の管理に携わった経験を持つことから、今回のプロジェクトにアサインされた。「水素エネルギーの話は白河工場にいた時から聞いていて、W.S.さんともよくその話をしていましたが、実際に水素エネルギー活用の可能性を一から調査していくと、能力的には問題のないことがわかってきたのです。では、白河工場に導入するなら何が必要なのか、さらに調査を進め、K.T.さんやW.S.さんといった白河工場環境管理課のメンバーと二人三脚で検討を進めていきました」。
水素エネルギーを用いたタイヤ製造に不可欠な水素ボイラーについては、M.M.が中心となって仕様検討を担った。「天然ガスに比べて水素は熱量が小さいことが懸念材料でした。蒸気の温度と圧力を規定範囲内でキープしながら生産しないとタイヤの品質に影響が出てしまうため、計画当初からボイラーをどうするかが一番のネックだったのです。国内で水素ボイラーを製造できる機械メーカーは数社しかありませんが、機械メーカーと打ち合わせを重ねる中、住友ゴムの生産仕様を満たせる水素ボイラーを開発できることがわかり、最終的にはオーダーメイドで水素ボイラーを発注することになりました。また、水素ボイラーは瞬間的に大量の水素が必要となるため、圧縮水素の受け入れ設備も導入することに。安全性を確保するため水素ボイラーの屋外設置を検討したり、水素は金属を脆くする性質があるため配管の材質を変えたりと、これまでの工場にはない設備仕様となりました」。
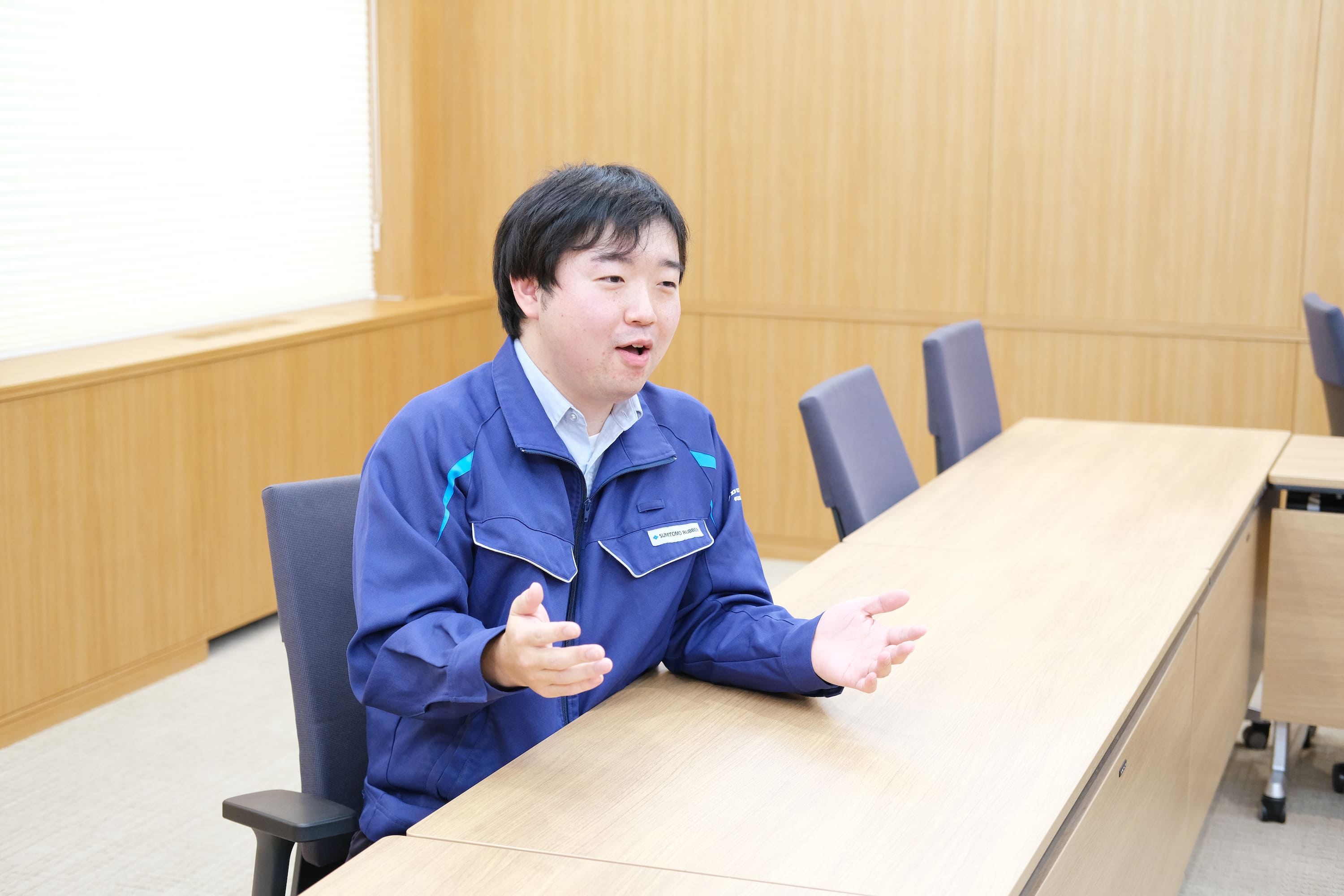
この前例のないチャレンジが、M.M.の大きなモチベーションになっていたという。「部署内には経験豊富な先輩方がいるので、これまでたいていの課題は先輩方のアドバイスで解決できました。でも、水素エネルギーの活用に関する知見はありません。そのため、課題が出れば自分が納得できるまで解決策の検討を重ねるなど、自らが考え、行動し、プロジェクトを形にしていけたことにやりがいを感じました。苦労の末に完成した水素ボイラーを初めて見た時は、実証実験の一つの節目とはいえ、大きな達成感がありました」。
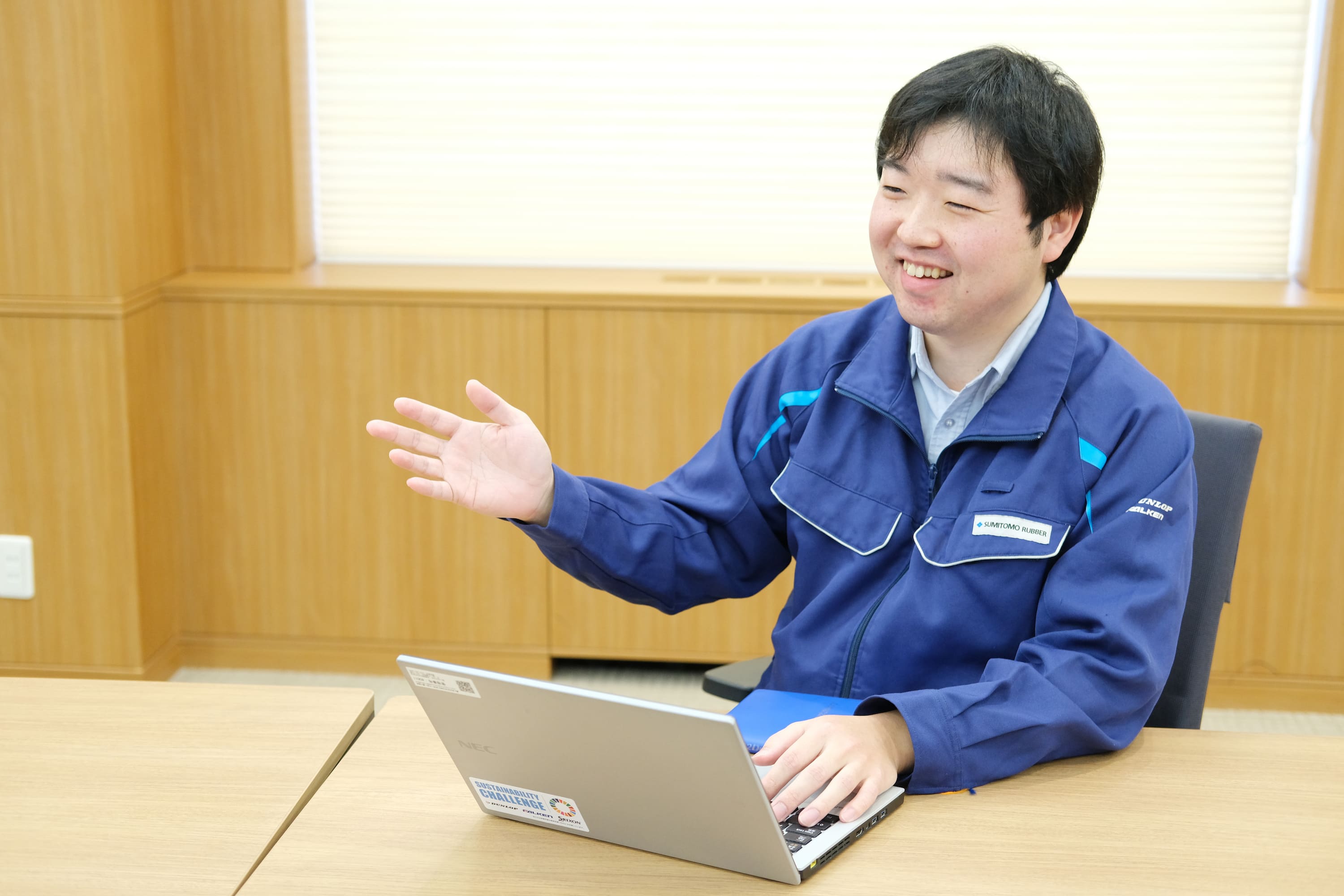
Chapter04実証実験を未来への一歩とするために
2023年1月、水素ボイラーが稼働し、水素エネルギーを燃料とするタイヤ製造の実証実験が本格化した。計画した通りにボイラーが稼働し、品質面で問題なくタイヤを製造できるのか。最終的には実証実験の結果で、水素エネルギー活用の可否まで判断することになる。
「導入した設備が安全に、安定して24時間稼働できるようにすることが当面の目標です」とW.S.。今回の実証実験で水素エネルギーを活用する技術を確立し、将来的には水素エネルギーが新しい環境価値として認められることにつなげたいと話す。「現段階では燃料としての水素は非常に高価で、それはタイヤの価格にも大きく影響することになります。でも、たとえば野菜なら有機栽培を選ぶ人がいるように、環境という価値で製品を選んでもらえるような時代が、SDGs の観点からも、すでに訪れ始めています。モビリティ社会にとって、環境は重要なテーマであり、タイヤメーカーが果たす責任は大きなものがあります。水素エネルギーの実用化にはまだまだ高いハードルがたくさんありますが、それらを飛び越えられる技術的な一歩を、今回の実証実験で実現していきたいですね」。
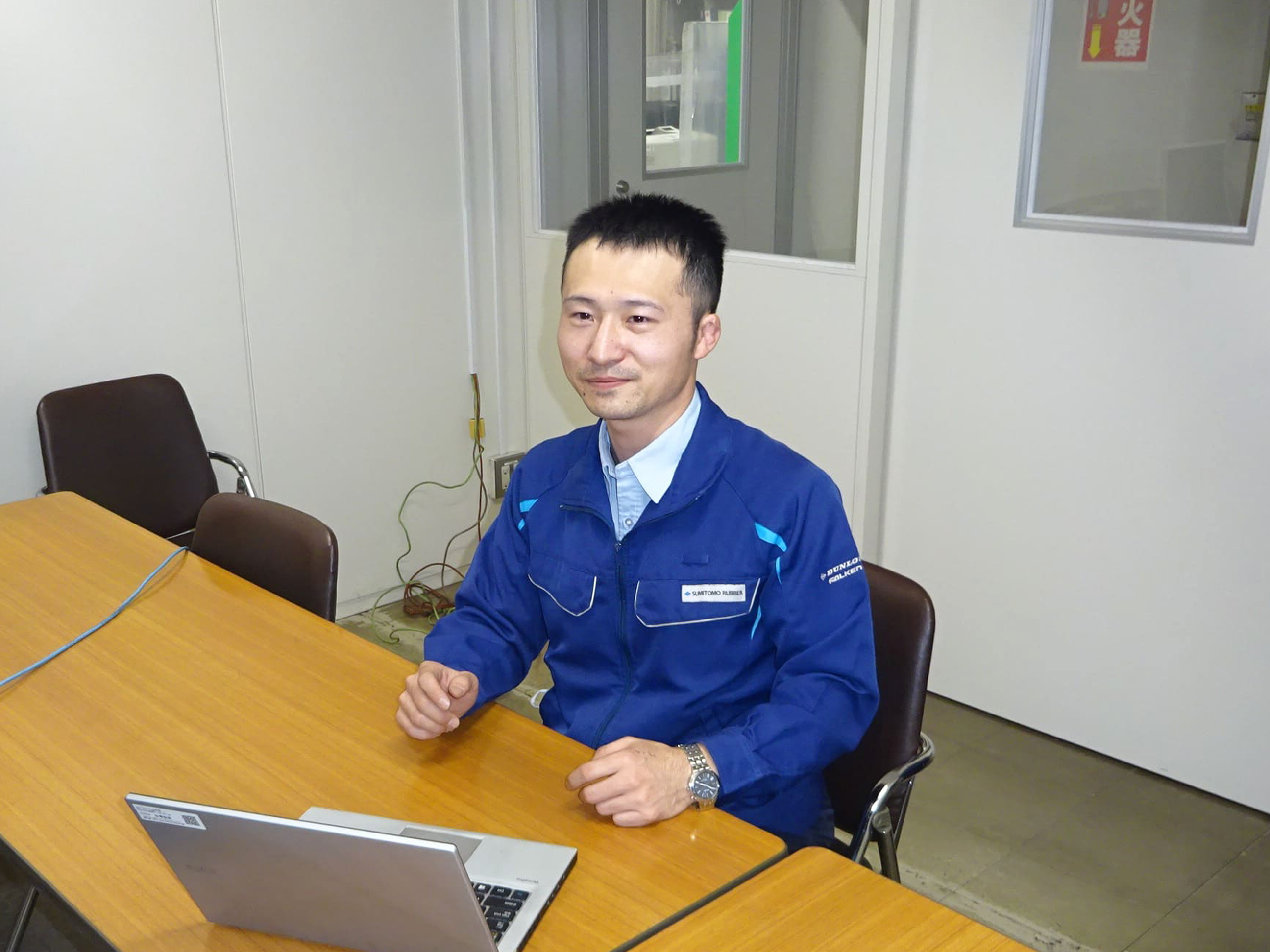
M.M.は今後水素エネルギーの導入時に課題が出れば、その課題解決のための調査・検討を行い、実証実験をアシストしていく立場となる。「今回の実証実験で得られる水素エネルギーに関する知見を、他の工場に技術展開することは当然視野に入れています。2030年までに、住友ゴム全体でカーボンニュートラルを実現できるような設備を各工場に導入する道筋を立てることが目標です」。さらに、設備技術部は全工場を俯瞰的に見て、物事を客観的に判断することが求められるため、そのスタンスで向き合っていきたいともM.M.は話す。「今は水素エネルギーの活用を目指していますが、アンモニア燃焼ガスタービン、高温ヒートポンプなど、カーボンニュートラルの実現にはあらゆる方法が考えられます。住友ゴムにとって、社会にとって、何が最善なのかを常に検討・提案していくことが、これからの私の役割だと考えています」。
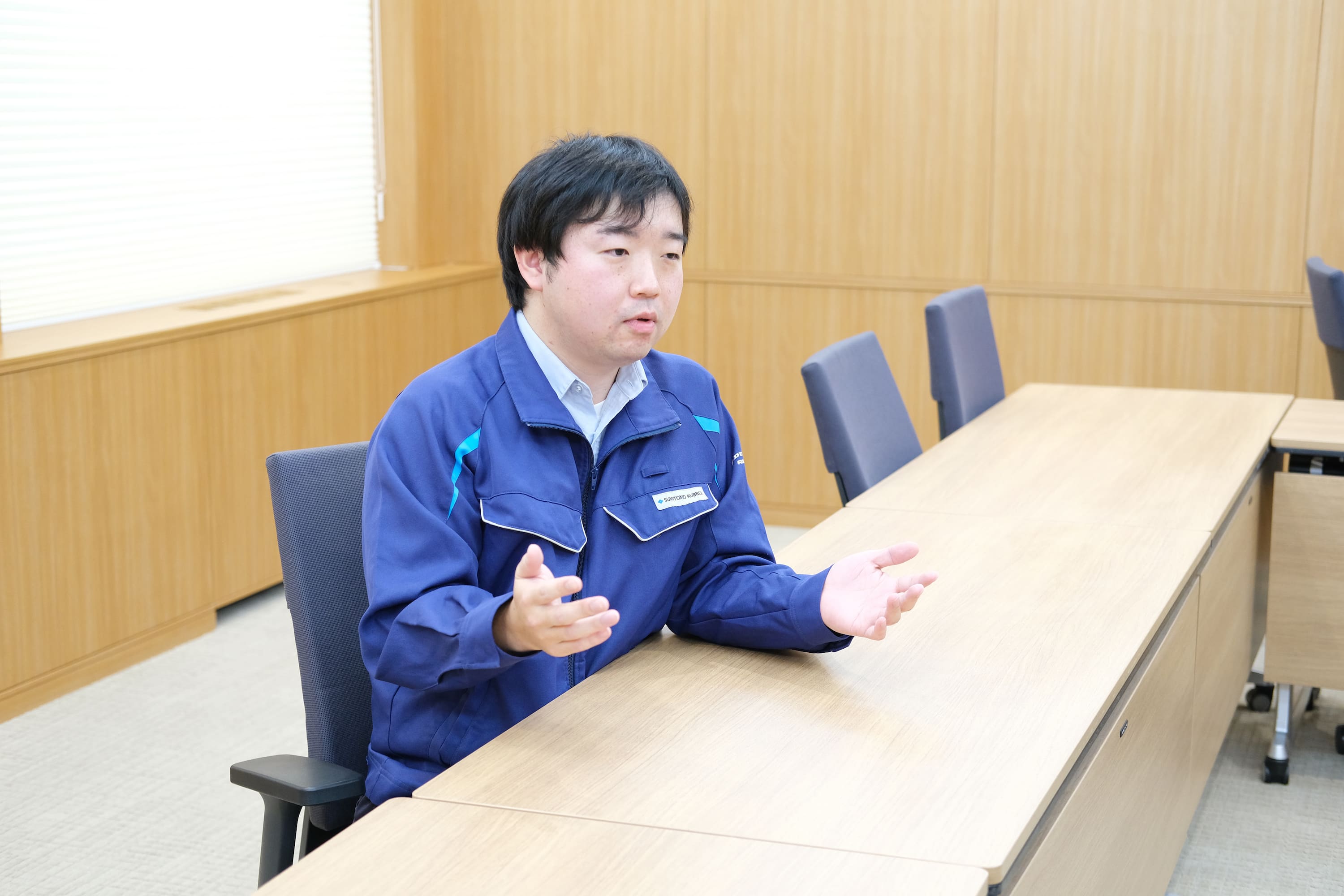
一方、福島県は福島新エネ社会構想を掲げるなど、次世代エネルギーの活用を推進する地域であり、白河市も「ゼロカーボンシティ宣言」を行っている。今回の実証実験は、福島県産水素を使う“白河モデル”の実現も見据えたものだ。「天然ガスと同じ熱量の水素を確保するためには、従来のトレーラーの約5倍の運搬量が必要であり、運搬の排ガスが増えたのでは意味がありません」とK.T.。その解決策の一つが、福島新エネ社会構想にもある水素の地産地消だ。福島県内で作った水素を使うことで運搬の排ガスや輸送コストを抑えることができ、白河工場での水素活用の取り組みを、各自治体で目指すまちづくりなどにつなげることができる。「計画当初は関東から水素を運ぶ案もありましたが、最終的には福島県内かつ50㎞圏内の郡山で製造する水素を使用することに決めました」とK.T.。今回NEDOの助成支援の対象となったのは、そんな“白河モデル”実現の一歩としても、大きな意味を持つことも背景にある。水素エネルギーの実用化に向けては、水素の需要が増え、水素自体のコストが下がるなど、社会的な要因も必要となるため、NEDOや地域とともに目指していきたいとK.T.は話す。「主任研究員として講演や展示会などで水素エネルギーの活用について話す機会が増えましたが、同じ製造業をはじめ、地域の多くの方々にも高い関心を持ってもらっています。その期待に応えていくことが私の目標です」。
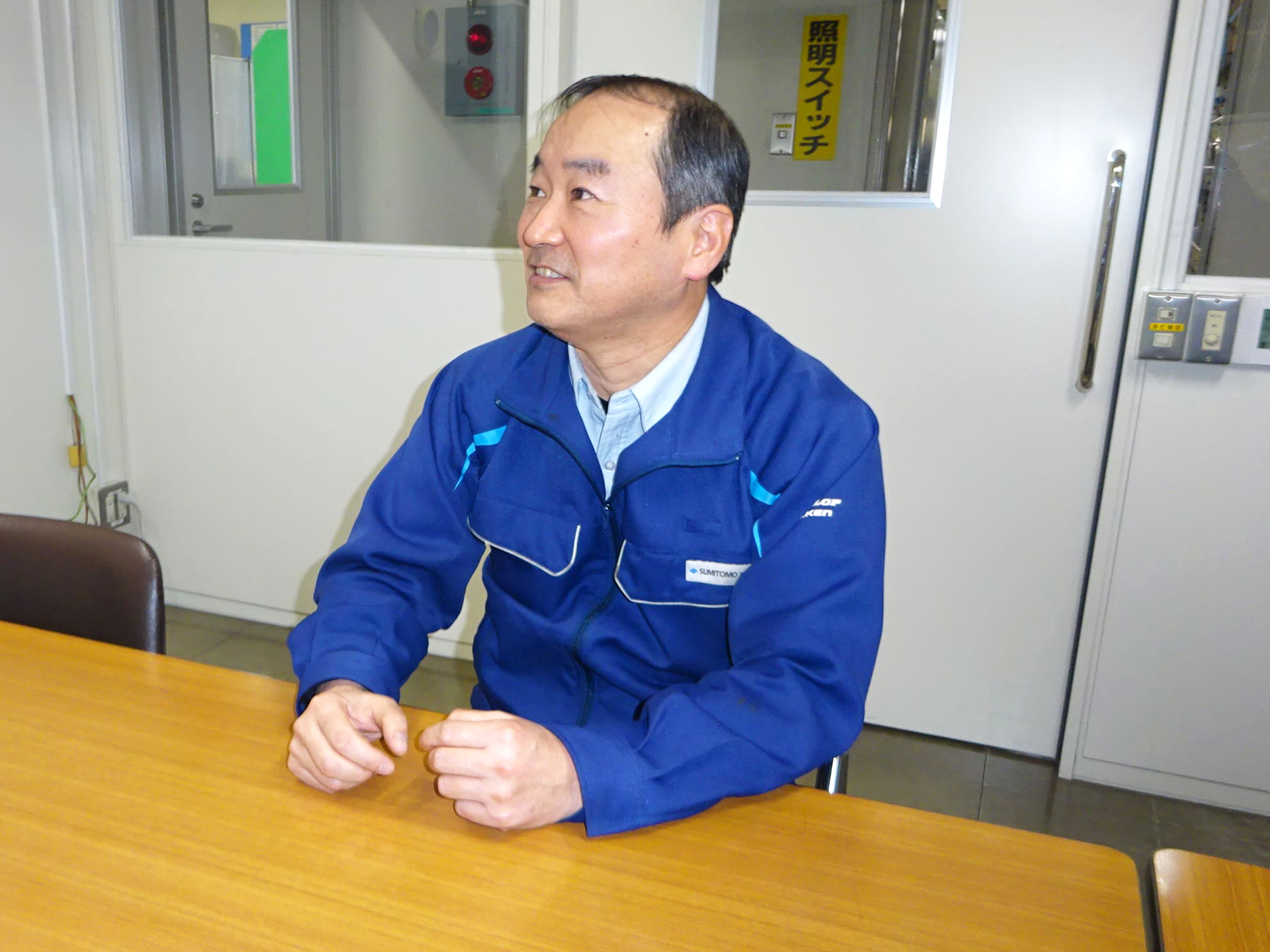
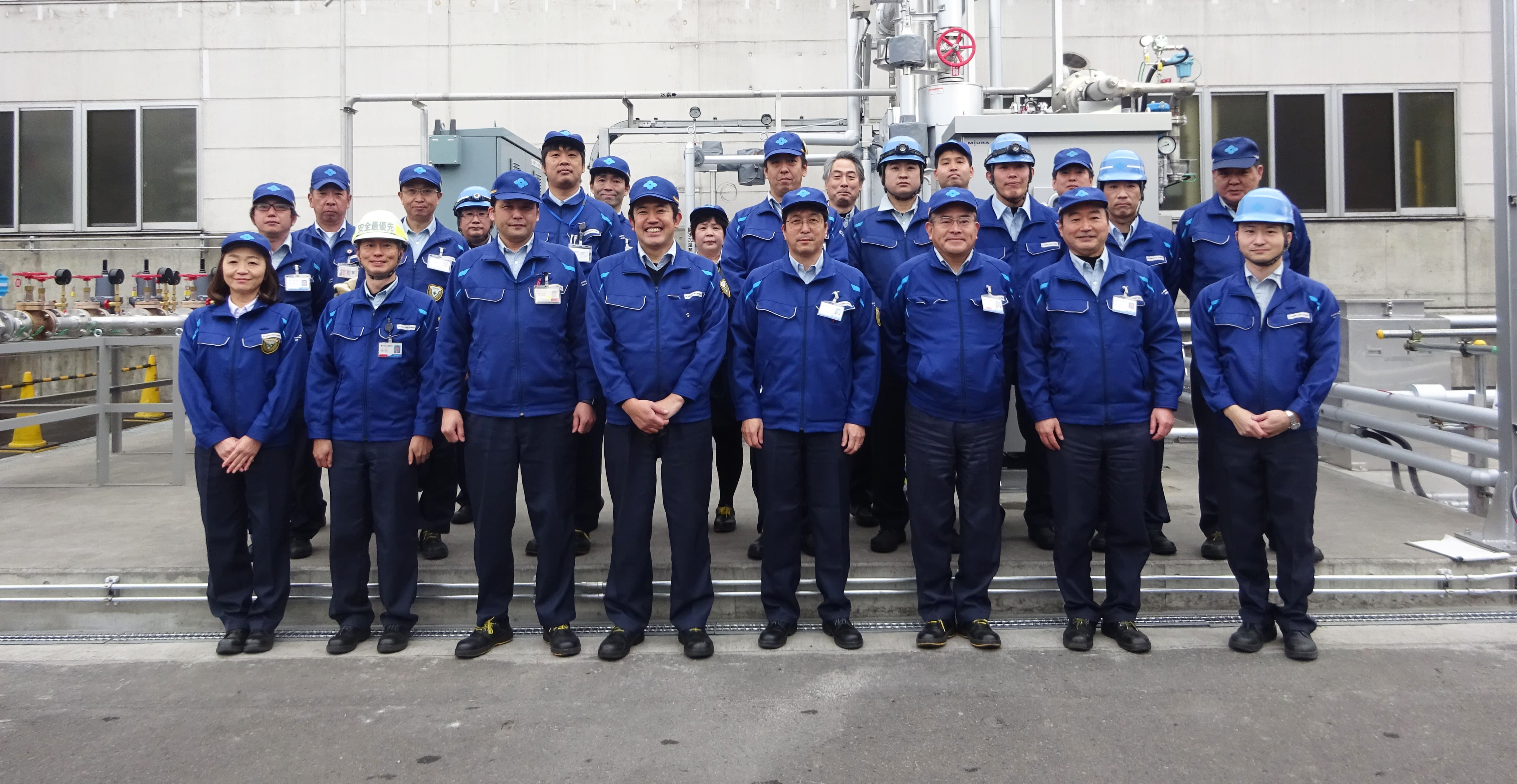
実証実験が動き始めたことで、高圧水素ボイラーの技術的な道筋は見えてきたが、実用化に向けての水素の供給量や供給方法、コストといった次の課題がより明確になってきた。「今後もたくさんの課題が出てくることでしょう。それでも、2050年までのカーボンニュートラルの実現は、目指すべき意義のある取り組みです。高いハードルをチーム一丸となって乗り越えられるように、社員の柔軟な発想力や感性を活かせる環境づくりに取り組み、私自身もまだまだ成長しながら、サポートしていきたいと考えています」。
[2024年追記]
2023年1月より、水素エネルギーと太陽光発電の自然エネルギーを活用した日本初の製造時カーボンニュートラル(Scope1,2)を達成した量産タイヤの生産を開始しました。
設備技術に関わる職種はこちら
職種紹介 設備技術